Vielleicht haben sich schon manche die Frage gestellt, wie der Antrieb des eigenen Elektroautos funktioniert oder was die Eigenheiten der Technologie sind. Dieser Beitrag hat zum Ziel, hierauf gut verständliche Antworten zu geben. Dabei bemühe ich mich, nicht zu sehr ins wissenschaftliche abzudriften, was Fachleute wiederum als ungenau empfinden könnten – ich bitte dies nachzusehen.
Für den Hintergrund (auch als Erklärung für die sparsamen Literaturangaben) möchte ich mich kurz vorstellen: seinerzeit habe ich Elektrotechnik studiert und mich dabei im Thema elektrische Maschinen vertieft. Des Weiteren habe ich bei zwei verschiedenen Automobilzulieferern an elektrischen Antrieben und deren Technologieentwicklung gearbeitet. In einem Fall handelte es sich um Hybridantriebe. So hoffe ich behaupten zu dürfen, dass ich einigermaßen im Thema stecke.
Wie funktioniert ein Elektromotor?
Die Wirkungsweise der meisten Elektromotoren beruht auf der Lorentzkraft. Ein stromdurchflossener Leiter erfährt in einem magnetischen Feld eine Kraft.
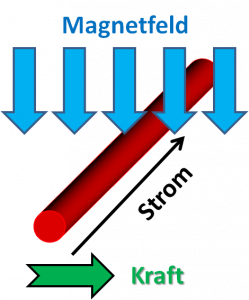
Einer meiner Professoren hat mal gesagt, dass man nur einen Draht mit Eisen zusammenbringen muss – dann wird sich schon irgendetwas bewegen. Prinzipiell stimmt das schon, hier möchte ich die Zusammenhänge aber ein wenig feiner auflösen.
Als stromdurchflossener Leiter wird fast immer ein Draht aus Kupfer verwendet, der zur Isolation mit Lack dünn beschichtet wird. Hierdurch erhält der Kupferlackdraht eine meist bräunliche Farbe. So wie Kupfer den Strom gut leitet, dient weichmagnetisches Eisen zur Führung des Magnetfeldes.
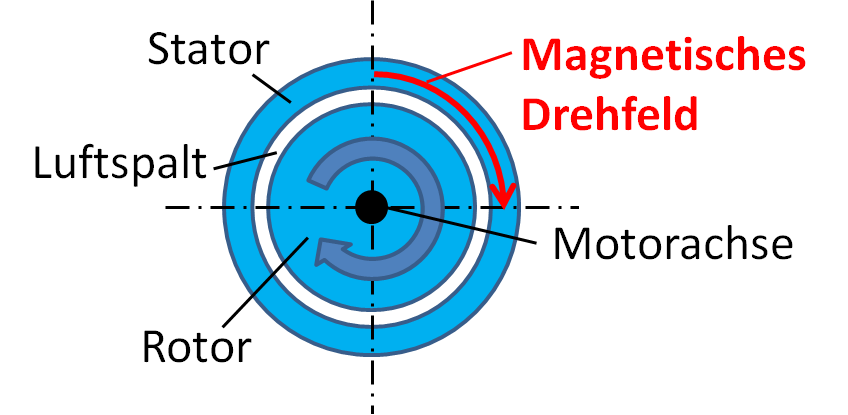
Der feststehende Teil eines Elektromotors wird als Ständer oder Stator bezeichnet, der bewegliche Teil als Läufer oder Rotor. Das Bild zeigt die prinzipielle Idee hinter drehenden Elektromotoren an Hand eines schematischen Querschnittes. Im Stator befindet sich eine Wicklung aus Kupferlackdraht, die meist aus drei getrennten Phasen besteht (im Bild oben nicht dargestellt). Schließt man diese Phasen an einen Drehstrom an (daher kommt auch dessen Name), so rotiert im Stator ein magnetisches Feld mit der Frequenz des Stromes.
Im Rotor wird ebenfalls ein Magnetfeld erzeugt, wie dies geschieht – darin unterscheiden sich die Verfahren. Das Magnetfeld des Rotors folgt der Bewegung des rotierenden Feldes im Stator, wodurch sich auch der Rotor dreht. Variiert man nun die Frequenz des Statorstromes, so kann die Drehzahl des Rotors ebenfalls eingestellt werden. Zu diesem Zweck benötigt der Elektromotor die Leistungselektronik.
Allgemeiner Aufbau
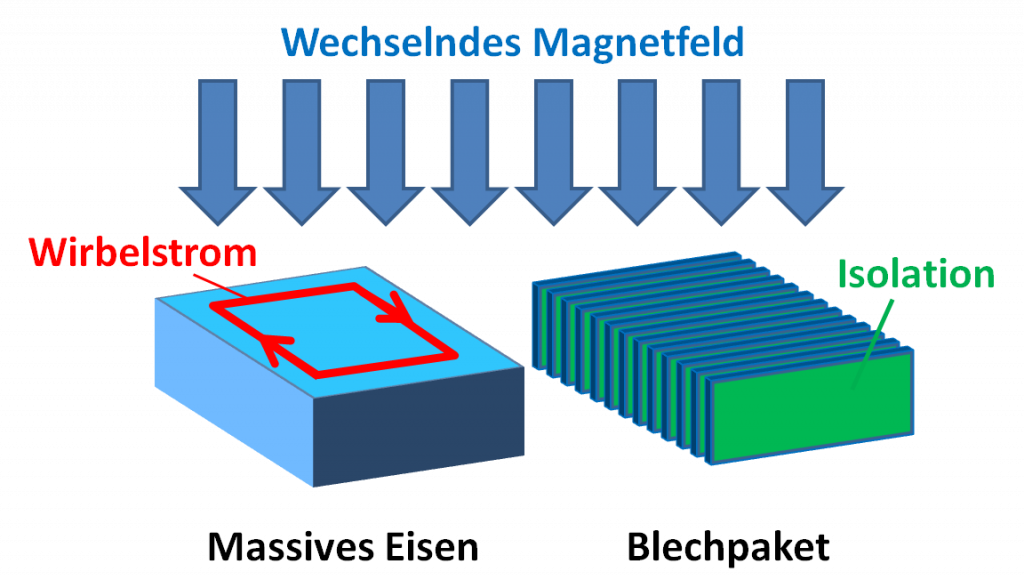
Im Eisen des Stators würden die magnetischen Wechselfelder Ströme verursachen, die zu Verlusten und einer Erwärmung sowie zur Reduzierung des Wirkungsgrades führen würden. Diese Ströme werden als Wirbelstrom bezeichnet. Um diesen zu vermeiden, besteht das Eisen aus gegeneinander isolierten Blechen, die zusammen das Blechpaket ergeben. Fast immer entstehen im Rotor ebenfalls magnetische Wechselfelder, weshalb auch hier Blechpakete verwendet werden.
Idealerweise wäre die Statorwicklung auf dem Umfang fein und gleichmäßig verteilt. Da sich das aber fertigungstechnisch nicht umsetzen lässt, werden die Kupferdrähte in Aussparungen des Blechpaketes, den Nuten, untergebracht. Die Bezeichnungen sollen an Hand der folgenden Darstellung verdeutlicht werden. Dabei st der Luftspalt der Einfachheit halber nicht gekrümmt, sondern gerade dargestellt.
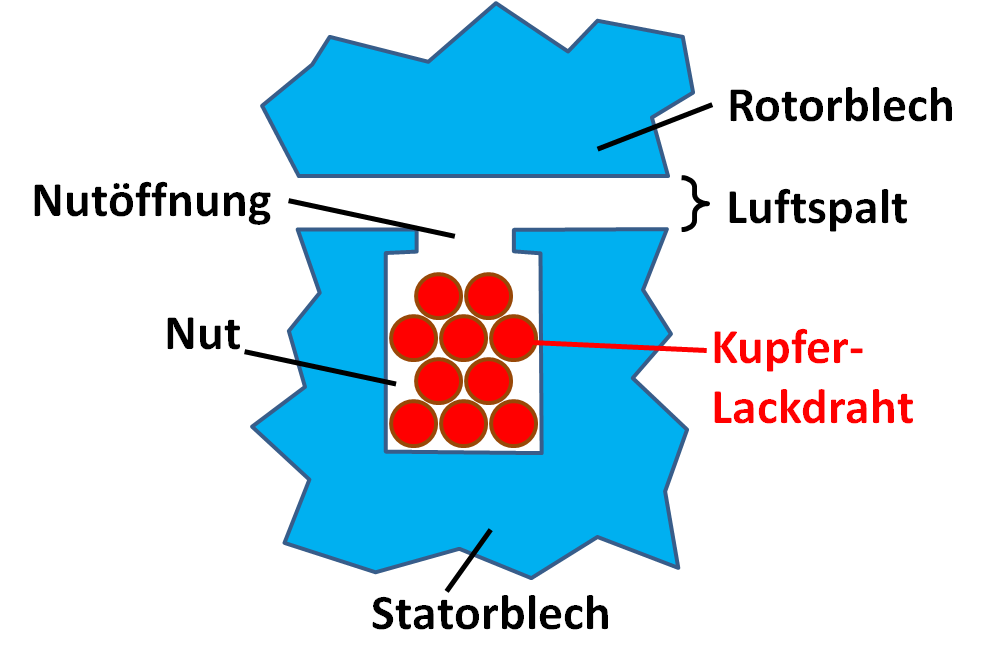
Aus der Anordnung in Nuten resultieren „Schmutzeffekte“, die Verluste hervorrufen. Diese basieren auf einer Verzerrung des ideal sinusförmigen Feldes, die als „Oberfelder“ (zum Sinus) bezeichnet werden. Durch geschickte Anordnung sowohl der Nuten als auch der Wicklung kann man viele dieser Oberfelder gezielt vermeiden. Das folgende Bild zeigt beispielhaft einen relativ praxisnahnen Stator mit 36 Nuten.
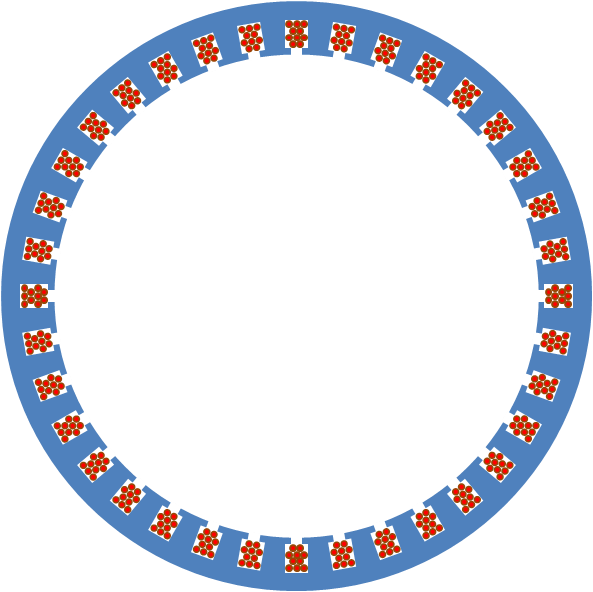
Motorleistung
Fährt man mit einem Hyundai Ioniq 150km auf der Autobahn und einem Durchschnittstempo von 100km/h, so verbraucht man in den 1,5 Stunden Fahrtzeit ca. 66% der Batteriekapazität. Dies entspricht einer Energie von 18,5kW/h und einem Energieverbrauch von ca. 12,3kWh/h. Geht man ferner von einem Wirkungsgrad (Batterie – Reifen) von 90% aus, so benötigt man im Schnitt etwa 13,7kW Leistung des Elektromotors.
Der Motor des Ioniq hat aber eine Maximalleistung von 88kW – wofür braucht man diesen Überschuss? Die Antwort ist: zum Beschleunigen. Dies bedeutet aber auch, dass der Antrieb eines Autos die allermeiste Zeit nur relativ gering beansprucht wird. Aus diesem Grund und um den Antrieb zu optimieren, legen die Hersteller den Elektromotor nicht wie meist bei industriellen Motoren für eine Dauerlast aus, sondern eher für eine große Überlast.
Dies betrifft insbesondere die Dimensionierung des Kühlsystems, welches sich vorwiegend an einer durchschnittlichen Leistung orientiert. Das ist unproblematisch, weil die Zeitkonstanten wegen der Wärmekapazität des Motors recht groß sind. Die Überlastfähigkeit ist also ein nicht unwichtiger Aspekt bei der Auslegung eines Elektromotors für Fahrzeuge.
Für den Tesla Model S P100D existieren Angaben zu nomineller bzw. Dauerlast von 158kW, wobei die Maximallast sagenhafte 515kW beträgt – also mehr als eine dreifache Überlastfähigkeit! Tesla selbst gibt ja auch zu, dass die Maximalleistung nur für eine sehr begrenzte Zeit abgerufen kann. Bei einer Beschleunigung von 0 auf 100km/h von unter 3s stellt sich aber auch gar kein anderweitiger Bedarf.
Varianten
Es existiert eine große Vielzahl verschiedener Wirkprinzipien bei Elektromotoren. Hier soll aber nur auf die für den Antrieb eines Elektroautos relevanten Varianten eingegangen werden. Dies sind der Asynchronmotor (ASM) und der Synchronmotor – sowie im nächsten Abschnitt der Reluktanzmotor.
Der Synchronmotor tritt in Varianten als Permanentmagnet erregter Synchronmotor (PSM) und als fremd- oder stromerregter Synchronmotor (SSM) auf. Der PSM erfreut sich einer weiten Verbreitung z.B im Hyundai Ioniq oder im VW eGolf. Die ASM-Variante wird von Tesla im Model S und X eingesetzt, während dagegen Renault mit dem Zoe auf die SSM-Variante setzt.
Der PSM
Synchronmotoren haben ein – bezogen auf den Rotor – statisches Magnetfeld. Dadurch dreht sich der Rotor immer mit der gleichen Geschwindigkeit wie das Drehfeld des Stators – also synchron. Beim PSM sind im Rotor Permanentmagnete angeordnet, die das statische Magnetfeld erzeugen. Die rote und grüne Farbe stehen für Nord- bzw. Südpol, also die Ausrichtung des Magnetfeldes.
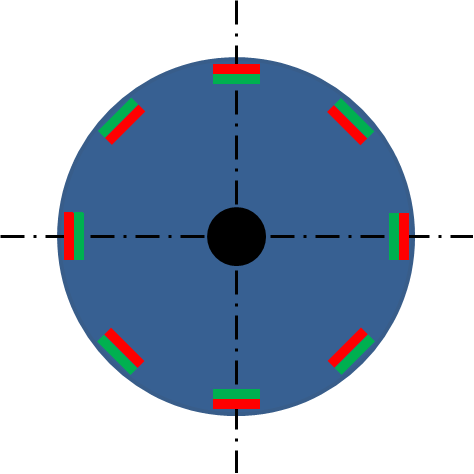
Zur Erzielung einer hohen Energiedichte kommen heutzutage ausschließlich Permanentmagnete aus Selten-Erd-Materialien wie Neodym-Eisen-Bor oder Samarium-Kobalt zum Einsatz. Dies ist ein nicht unerheblicher Kostenfaktor des gesamten Elektromotors.
Man könnte denken, dass Nord- und Südpol der Permanentmagnete durch die vollständige Einbettung ins Blechpaket magnetisch kurzgeschlossen sind. Hier wird aber der sonst störende Effekt der magnetischen Sättigung (an der schmalsten Stelle des Blechquerschnittes) im positiven Sinne ausgenutzt. Sättigung tritt ein, wenn das Blech ein zu „dichtes“ Magnetfeld leiten soll. Auf diese Weise steht bei der dargestellten Anordnung der Hauptteil des Magnetfeldes am Luftspalt zur Verfügung.
Bei der Produktion ist die Handhabung der spröden Magnete eine Herausforderung, weshalb diese manchmal auch erst nach der Montage im Rotor aufmagnetisiert werden. Meist können nur einfache Geometrien wie etwa quaderförmige Magnete verwendet werden, was die geometrische Optimierung des Rotors einschränkt.
Die Ansteuerung eines PSM ist relativ einfach. Dies zeigt sich u.a. im Generatorbetrieb (bei der Rekuperation). Wird der Rotor eines PSM gedreht, so induziert das Magnetfeld Spannungen in der Wicklung des Stators, die man direkt nutzen kann. In bestimmten Betriebssituationen ist es aber auch hinderlich, dass sich das Magnetfeld des Rotors nicht „abschalten“ lässt.
Varianten ohne Permanentmagneten
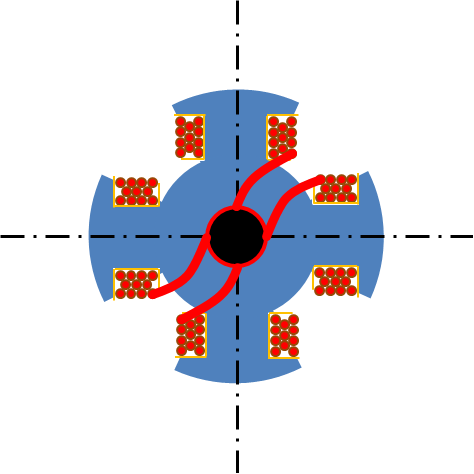
Beim strommerregten Synchronmotor (SSM) wird das statische Magnetfeld im Rotor durch ein eigenes, relativ einfaches Spulensystem erzeugt. Das Bild zeigt schematisch, wie die Rotorwicklung mit einem der Schleifringe verbunden ist. Der Schleifring ist ein geschlossener Ring auf der Achse (natürlich zu dieser isoliert), der über Schleifkontakte mit Gleichstrom versorgt wird.
Ein Vorteil des SSM gegenüber dem PSM ist die Variabilität des Rotor-Magnetfeldes. Außerdem besteht nicht wie beim PSM die Gefahr, dass die Permanentmagnete bei Überlast entmagnetisiert werden. Beim Zoe wird der Motor für das Laden sogar als Transformator verwendet. Nachteilig sind die Schleifringe, die einem gewissen Verschleiß unterliegen, zusätzliche Bauteile erfordern und außerdem den gesamten Motor verlängern.
Die Drehzahl eines Asynchronmotors (ASM) liegt immer unterhalb der des Drehfeldes im Stator, im Leerlauf aber sehr dicht daran. Dieser Unterschied wird als „Schlupf“ bezeichnet. Der Stator sieht identisch aus wie bei Synchronmotoren (SM). Der Rotor besteht aus einem Blechpaket und einer kurzgeschlossenen Wicklung in Nuten. In dieser Wicklung wird durch das Drehfeld des Stators eine Spannung erzeugt, die ihrerseits wiederum ein Magnetfeld aufbaut, welches in Wechselwirkung zu dem des Stators tritt.
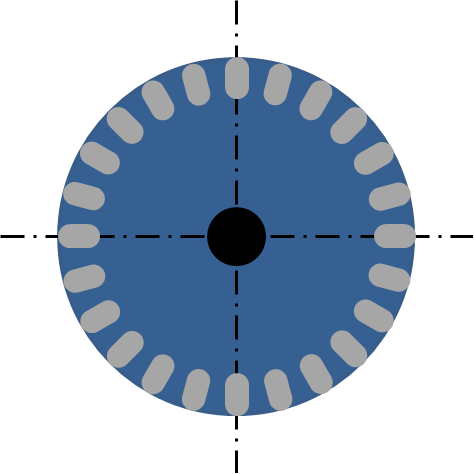
Wenn man also den Stator eines ASM von der elektrischen Versorgung trennt, kann man den Rotor ohne Kraftaufwand drehen (der SSM hat im Vergleich hierzu durch die Schleifringe ein wenig mehr Reibung). Um den ASM als Generator zu betreiben, muss zunächst ein Magnetfeld erzeugt werden, die Ansteuerung ist dadurch ein wenig komplexer als beim SM. Der Vorteil eines ASM in industriellen Anwendungen beruht auch auf seinem selbstständigen Anlauf bei Netzfrequenz (50Hz). Dieser Vorteil kommt im Elektroauto nicht zum Tragen, da die Drehzahl jederzeit angepasst werden muss.
Der Rotor im ASM benötigt wie der SSM keine teuren Permanentmagnete. Die Rotorwicklung ist sehr einfach und kostengünstig aufgebaut: die Nuten des Blechpaketes werden in einem Druckgussverfahren mit massivem Aluminium gefüllt. Im gleichen Prozess werden auch die Kurzschlussringe beidseitig an den axialen Enden des Rotors erzeugt, die die Aluminiumleiter in den Nuten miteinander verbinden. Eine Isolation wird nicht benötigt – es genügt, dem Strom durch die Aluminiumleiter quasi eine Vorzugsrichtung zu geben.
Durch diese einfache Herstellung eines ASM-Rotors sind die gestalterischen Möglichkeiten der Nuten im Blechpaket nahezu unbegrenzt. Hierdurch kann der Rotor leicht und bei identischen Kosten optimiert werden, um z.B. Verluste durch Oberfelder zu minimieren. Ein großer Nachteil des ASM liegt aber in der geringeren Leistungsdichte. Das bedeutet, dass bei gleicher Leistung der ASM größer ausfällt und damit auch schwerer ist als ein Synchronmotor.
Sonderfall Reluktanzmotor
Über den im Tesla Model 3 verbauten Motor existieren widersprüchliche Aussagen. Die einen bezeichnen ihn als Reluktanzmotor, andere als PSM. Eventuell hilft ein Zitat weiter:
„AC induction front & switched reluctance, partial permanent magnet rear. Silicon Carbide inverters in both. Performance drive units are lot sorted for highest sigma output & get double the burn-in.“
(Elon Musk, 3:41 AM – May 20, 2018)
Ich deute diese Aussage so, dass in der optional zweimotorigen Ausstattung des Model 3 vorne ein ASM und hinten besagter Reluktanzmotor mit Permanentmagneten zum Einsatz kommen.
Reluktanz ist ein Ausdruck für den magnetischen Widerstand und ein Indiz dafür, dass das Wirkprinzip ein wenig anders ist als bei den bisher beschriebenen Varianten. Es dürfte bekannt sein, dass Permanentmagnete oder auch stromdurchflossene Spulen Eisen anziehen. Das zu Grunde liegende Prinzip ist also nicht die Lorentzkraft, sondern der Magnetismus.
Bei einem (echten) Reluktanzmotor besteht der Rotor nur aus Eisen bzw. dem Blechpaket, welches aber ausgeprägte Strukturen (Zähne) ausweist. In dem Beispiel wird ein dreiphasiger Motor (violett, blau, schwarz) betrachtet.
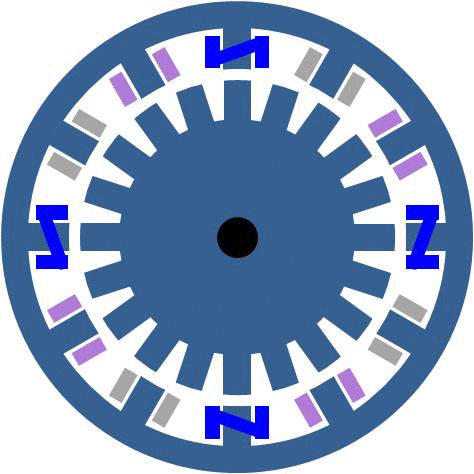
Wenn z.B. die schwarze Phase erregt ist, richten sich die Zähne des Rotors an denen der schwarzen Phase im Stator aus. Wird eine der anderen Phasen erregt, bewegt sich der Rotor (um einen Winkel von hier 5°) in die entsprechende Richtung.
Bekannt sind derartige Ausführungen etwa als Schrittmotor, wo es um eine präzise Positionierung geht. Schaltet man die Phasen fortlaufend so wie ein Drehfeld, so können auch kontinuierliche Bewegungen erzielt werden. Die Leistungsdichte ist allerdings sehr gering und der Aufwand zur Ansteuerung recht hoch, was aber heutzutage nicht mehr so bedeutsam ist.
Ein klarer Vorteil des Reluktanzmotors ist der äußerst einfache und damit sehr robuste Aufbau des Rotors. Bei der hier dargstellten Ausführung muss das Feld des Stators zehnmal nacheinander durchgeschaltet werden (bzw. das Drehfeld 10 Umdrehungen absolvieren), bis der Rotor eine Umdrehung vollzieht. Dadurch erhält man eine gute Untersetzung und kann das Getriebe entsprechend einfacher ausführen.
Hybridmotor
Wenn man nun die Zähne des Rotor durch Permanentmagnete ersetzt, ändert sich vieles. In der Praxis müssen die Permanentmagnete gegen Fliehkräfte geschützt werden, aber hier soll nur das Prinzip erläutert werden.
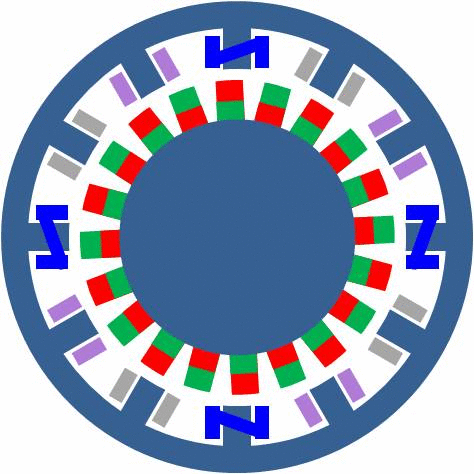
Mit Permanentmagneten kann dieser Motor auch als Generator betrieben werden, auch die Leistungsdichte steigt signifikant. Von außen ist selbst bei ausgeschalteter Wicklung ein hohes Rastmoment spürbar – meist kann man den Rotor gar nicht mehr von Hand drehen. Dieser Effekt ist für die Anwendung als Schrittmotor sogar explizit erwünscht.
Meist wird ein derartiger Aufbau als Hybridmotor bezeichnet, weil man das Reluktanzprinzip mit dem des PSM kombiniert. Genausogut könnte man den Motor auch als „gezahnten“ PSM (mit ausgeprägten Zähnen im Rotor) bezeichnen. Sowohl von der Performance als auch von der Ansteuerung her unterscheidet sich der Hybridmotor nicht signifikant vom PSM.
Die Bilder vom Motor des Model 3, die ich kenne (z.B. teslamotorsclub.com), lassen einen nur gering geometrisch ausgeprägten Rotor erkennen, so dass ich diese Bauform eher als PSM bezeichnen würde. Außerdem lassen die zahlreichen Statornuten keine stark variierende Reluktanz vermuten – auch der Stator sieht wie bei üblichen PSM aus.
Allerdings könnte es natürlich aktuellere Ausführungen geben, die noch nicht demontiert und dokumentiert wurden. Ich vermute aber eher, dass Elon Musk mit dem oben aufgeführten Zitat ein wenig die Gerüchteküche anfeuern und so für Publicity sorgen wollte…
Motorgeometrie
Elektromotoren können geometrisch sehr unterschiedlich sein: die runde Grundform kann zwischen lang gestreckten Zylindern bis hin zu scheibenartigen Formen variieren. Vorteil der lang gestreckten Form ist der größere Anteil des Aktivteils. Denn nur das Blechpaket mit den Drähten in den Nuten kann ein Drehmoment erzeugen. An den axialen Enden müssen die Drähte der Nuten aber noch im sog. Wickelkopf miteinander verbunden werden. Hinzu kommen auch noch Lagerschilde etc.
Scheibenartige Aufbauten können durch den größeren Umfang aber mit deutlich mehr Nuten versehen werden, wodurch die Polzahl erhöht werden kann. Dies bedeutet, dass sich über den Umfang des Motors magnetische Nord- und Südpole vielfach wiederholen können. Dadurch ist die Motordrehzahl bei gleicher Drehstromfrequenz geringer, das Drehmoment aber umso höher.
Grundsätzlich kann der Stator sowohl um den Rotor herum oder innenliegend angeordnet sein (Außenläufer). Bei Antrieben für Elektroautos hat sich aber die Anordnung als Innenläufer durchgesetzt. Hauptgrund dürfte der bei Außenläufern höhere Aufwand hinsichtlich der Lagerung des Rotors sowie die höheren Fliehkräfte sein.
Problem Verlustwärme
Wie bereits angedeutet ist der Kupferlackdraht nur sehr dünn beschichtet. Würde dieser Draht ungeschützt in den Nuten des Blechpaketes verlegt werden, so wären Isolierungsschäden und Kurzschlüsse garantiert. Dies gilt insbesondere für die axialen Enden, wo der Draht an den scharfen Kanten der Nut herum in den Wickelkopf geführt werden muss. Folglich werden zusätzliche Isolationsschichten verwendet, die meist aus speziellem Papier oder Kunststoff bestehen.
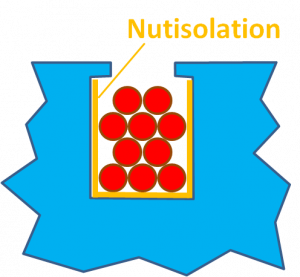
Der Wirkungsgrad von Motoren für Elektroautos ist mit oft mehr als 90% sehr hoch. Das bedeutet aber dennoch, dass im Elektromotor 10% der Leistung als Wärme umgesetzt werden. Dies entspricht bei einer aufgenommen Leistung von 50kW einer Verlustwärme von 5kW! Diese Wärme entsteht größtenteils in der Wicklung des Stators und muss effektiv abgeführt werden, um Schäden zu vermeiden.
Die oben notwendige elektrische Isolierung stellt aber unglücklicherweise auch eine gute Wärmeisolation dar, wodurch die Wärmeabfuhr aus der Wicklung in das Blechpaket erschwert wird. Der Rotor ist manchmal beidseitig axial am Ende mit paddelförmigen Strukturen versehen, die zur Kühlung im Wickelkopf beitragen.
Diese Methode der Kühlung reicht aber oft nicht aus, sondern muss durch eine Ableitung der Wärme aus den Nuten heraus unterstützt werden. Dies geschieht durch eine spezielle Vergussmasse, um alle Hohlräume auszufüllen. Das Besondere am Verguss ist die Notwendigkeit einer elektrischen Isolation bei gleichzeitig guter Wärmeleitfähigkeit.
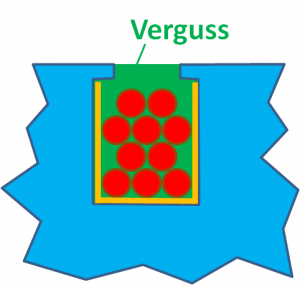
Der Verguss kann zwar die Wärmeleitung verbessern, aber selbst zu einem neuen Problem werden. Der Grund hierfür sind die extremen Temperaturen bei einem Auto. Bei sehr tiefen Temperaturen – meist werden bis zu -40°C angenommen – verhält sich der Kunststoff wie Glas. Außerdem dehnt sich das Blechpaket deutlich weniger als der Verguss aus, wodurch dieser aufreißen und so die gesamte Isolation der Wicklung gefährden kann. Meist kann man aber mit einer gewissen Neigung zu Rissen im Verguss noch leben, v.a. wenn das Eindringen von Wasser unwahrscheinlich erscheint.
Weitere Technologien
Die einzelnen Bleche für die Blechpakete werden aus Tafeln ausgestanzt und anschließend aufeinander gefügt. Diese Verbindung muss hohen Kräften standhalten – schließlich soll das Motordrehmoment übertragen werden. Zwei Verfahren sind weit verbreitet: das mechanische Verknüpfen miteinander (ähnlich dem Vernieten) sowie das Verkleben der einzelnen Bleche untereinander, wobei der Kleber unter Hitze aufgeschmolzen wird. Die Isolierung der einzelnen Bleche untereinander besteht grundsätzlich aus einer dünnen Lackschicht.
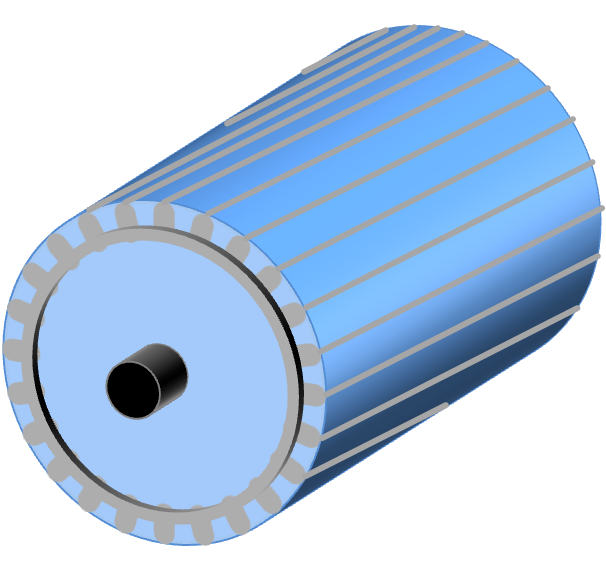
Eine wirkungsvolle und zugleich einfache Methode zur Unterdrückung magnetischer Oberwellen ist das sog. Schrägen der Rotornuten. Das obige Bild veranschaulicht dieses Design an ein einem ASM-Rotor. Wie man erkennen kann, sind die Nuten über die axiale Länge des Rotors nicht parallel zur Drehachse, sondern verdreht hierzu. Beim Rotor eines PSM wird dieses Verfahren häufig ebenfalls eingesetzt, allerdings nicht „stufenlos“ wie beim ASM und damit nicht ganz so wirksam. Der Rotor mit Permanentmagneten ist stattdessen axial unterteilt und die Teile leicht zueinander verdreht.
Eine Schlüsseltechnik betrifft die Verbindungstechnik der Kupferdrähte untereinander und/oder mit den äußeren Anschlüssen. Weichlöten kann die Anforderungen hinsichtlich Temperaturfestigkeit nicht erfüllen, so dass z.B. Hartlöten oder verschiedene Schweißverfahren eingesetzt werden. Da die Verbindungstechnologie oft fehleranfällig ist, wird der Prozess meist zu 100% überwacht. Beim Widerstandsschweißen betrifft dies z.B. den Einsinkweg der Elektroden sowie die Schweißstrom-Messung.
Prinzipiell wäre das Laserschweißen elektrischer Verbindungen ein ideales Verfahren, weil dabei in kurzer Zeit und örtlich gut aufgelöst Energie eingebracht wird. Die umgebende Isolation würde also nicht verbrennen. Leider reflektiert Kupfer die Strahlung üblicher Laser. Prinzipiell konnte die Machbarkeit zwar nachgewiesen werden, das Verfahren bleibt aber aufwändig und störanfällig.
Spezielles Thema: die Wicklung
Grundsätzlich möchte man in den Nuten des Stators möglichst viel Kupfer unterbringen (dies gilt auch für den Rotor des SSM). Allerdings kann hierfür die Nut nicht wie beim Rotor des ASM massiv gefüllt werden. Ebenso sind hochkant angeordnete Kupferbänder ungeeignet.
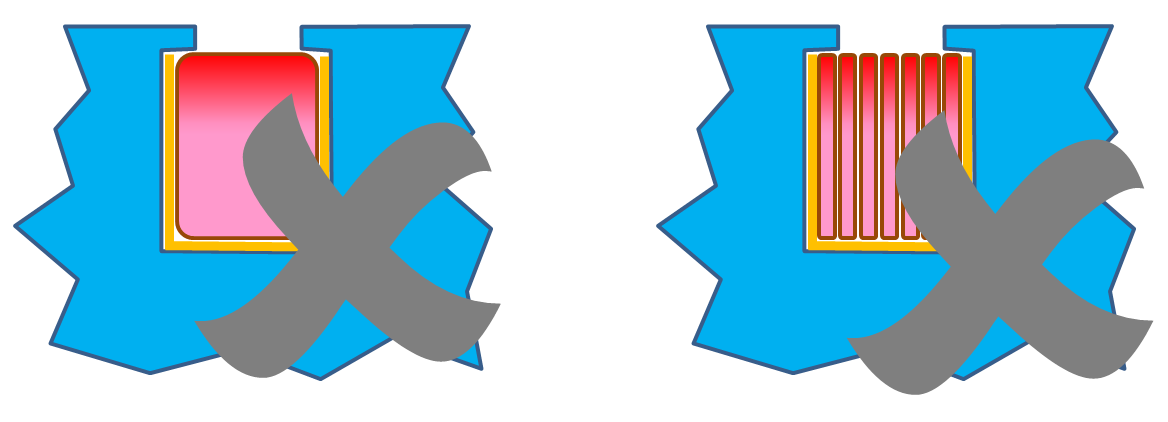
Der Grund hierfür ist der frequenzabhängige Effekt der sog. Stromverdrängung, wodurch der Strom hauptsächlich in der Nähe des Luftspaltes fließt (rot) und der Großteil des Leiters quasi ungenutzt bleibt (rosa).
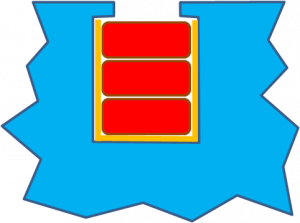
Eine Möglichkeit für einen hohen Füllgrad an Kupfer in der Nut zeigt das obige Bild. Diese massiven Leiter sind aber unflexibel, weshalb sie als Formteile in die Nut geschoben werden müssen. Das führt wiederum zu einer Vielzahl an Verbindungen im Wickelkopf. Noch nachteiliger sind aber der hohe Aufwand und die damit verbundenen Kosten im Vergleich zu anderen Wickelverfahren.
Wickeltechnologien
Je einfacher und kostengünstiger ein Wickelverfahren für Kupferlackdrähte ist, desto geringer fällt der Füllgrad in der Nut aus. Hier gilt es also einen Kompromiss zu finden. Einfache Verfahren führen oft zu Drahtkreuzungen in der Nut und zu einer sog. chaotischen Anordnung. Eine ideale Lage der Drähte zueinander in der Form der dichtesten Kugelpackung wird in der Praxis nie erreicht, man versucht aber sich daran anzunähern.
Ein Verfahren ist z.B. die Nadelwicklung bei der ein Kupferlackdraht über eine Art Düse in die Nutöffnung CNC-gesteuert gelegt bzw. gezogen wird. Zur definierten Drahtführung werden manchmal auch speziell geformte Kunststoff-Nutisolierungen verwendet. Noch aufwändiger ist das Einziehen, wo die Wicklung außerhalb des Stators geformt wird und in einem Stück und mit hoher Kraft in das (isolierte) Blechpaket eingezogen wird.
Häufig wird auch ein komplett anderer Ansatz verfolgt, indem nicht der komplette Stator, sondern nur Teile davon (Zähne) bewickelt werden. Der Stator wird dann später aus einer Vielzahl von Zähnen zusammengesetzt. Die einzeln bewickelten Zähne werden dann auch elektrisch miteinander verbunden. Der Vorteil des Verfahrens liegt auf der Hand: die Zähne können kostengünstig und präzise, d.h. mit sehr gutem Füllfaktor, bewickelt werden.
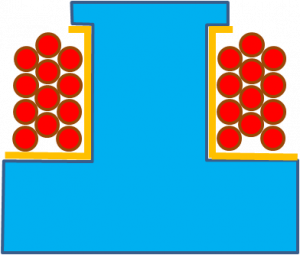
Nachteilig ist dagegen die Einschränkung bei der Verteilung von Phasen in die Nuten, was Verluste durch Oberfelder nach sich zieht. Hinzu kommen Verluste im Blechpaket, da zusätzliche Fügespalte nicht vollständig vermieden werden können. Auch die aufwändige Handhabung beim Zusammenfügen der einzelnen Zähne ist negativ. Um dieses Problem zu entschärfen, werden die Zähne oft auch am äußersten Umfang des Blechpaketes durch dünne Stege zusammengehalten – das Blechpaket wird dann später „zusammengerollt“.
Häufig wird für die Wicklung ein spezieller Draht, der sog. Backlackdraht verwendet. Hier befindet sich auf dem Kupferlackdraht eine zusätzliche Schicht, die durch Wärmeeinwirkung angeschmolzen wird und beim Erkalten zum Verkleben der Drähte untereinander und mit der Isolation führt. Dies erleichtert die Handhabung und erhöht die Stabilität.
Bauraum ist in jedem Fahrzeug knapp, weshalb z.B. ein ausladender Wickelkopf nicht nur wegen des erhöhten Widerstandes nachteilig ist, sondern auch wegen des längeren Motors. Daher wird der Wickelkopf des Stators häufig verpresst und geformt, um ihn kompakter zu gestalten. Dabei muss selbstverständlich eine Beschädigung der Isolation vermieden werden.
Allgemein können bei der Herstellung und Integration der Wicklung in das Blechpaket viele Dinge schief laufen. Nicht durchgängig hochstromfähige Verbindungen, Kurzschlüsse zum Blechpaket und einzelner Drähte untereinander sind dabei die typischen Fehler. Aus diesem Grund erfolgt ein aufwändiger Test für jeden Elektromotor (100%-Prüfung), bevor das Aggregat weiter verarbeitet wird.
Der Stator wird dabei elektrisch hinsichtlich Widerstand und Isolation geprüft. Nach Fertigstellung des kompletten Motors folgt dann noch eine komplexe Prüfung sowohl elektrischer, akustischer als auch mechanischer Eigenschaften. Durch diese Kombination an Tests gelingt eine wirkungsvolle Erkennung von problematischen Motoren.
Motorperipherie
Ein preisgünstiges Verfahren zur Befestigung von Blechpaketen etwa im Statorgehäuse ist das Schrumpfen. Hierbei wird das Gehäuse auf meist mehrere hundert Grad erwärmt, wodurch es sich ausdehnt. Das Blechpaket wird bei Raumtemperatur eingefügt und nach dem Schrumpfen bzw. Erkalten des Gehäuses sind beide Teile stabil und dauerhaft miteinander verbunden. Selbstverständlich sind auch einfache Befestigungen wie Schrauben möglich. Oft wird das Gehäuse mit Kühlwasser durchflossen.
Nach meiner Wahrnehmung scheint sich der Einbau von Elektromotoren in speziell dafür vorgesehene Gehäuse beim Elektroauto durchzusetzen. Dies hat mehrere Vorteile: man kann so die Wicklung leichter vor Beschädigung oder dem Eindringen von Wasser schützen. Der Motor kann effektiv und auf vielfältige Weise gekühlt werden – z.B. über Öl, Kühlwasser oder auch einfach durch Kühlrippen am Gehäuse, so wie bei Industriemotoren. Schließlich können auch einfach weitere Anbauteile integriert werden.
Ein wichtiges Zubehör im direkten Zusammenspiel mit einem Elektromotor ist die Erkennung der Rotorlage. Hierfür gibt es mehrere Möglichkeiten und Verfahren. Eines davon ist die Magnetfeldmessung mit Hilfe eines Hallsensors. Dies funktioniert sehr effektiv bei Rotoren, die ohnehin Permanentmagnete enthalten, z.B. beim PSM. Der Hallsensor ist ein Halbleiterplättchen, welches von einem kleinen Messtrom durchflossen wird, der durch das Magnetfeld je nach Stärke und Ausrichtung abgelenkt wird. Diese Ablenkung kann extern als Hallspannung gemessen werden.
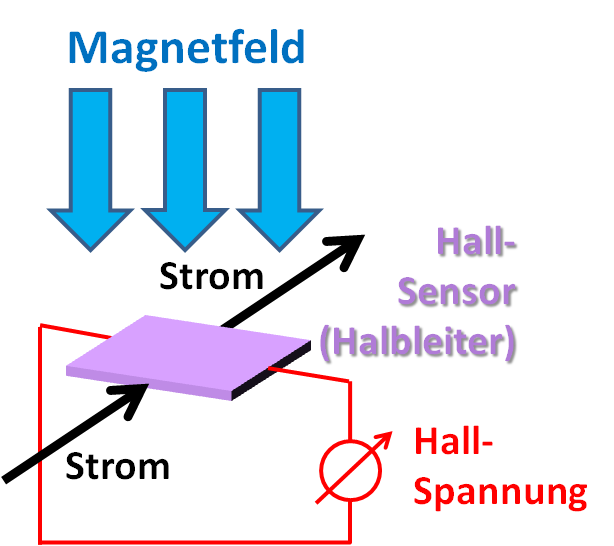
Andere Verfahren zur Ermittlung der Rotorlage wie z.B. Resolver sind präziser aber auch aufwändiger. Die meisten funktionieren prinzipiell ähnlich wie kleine Generatoren, liefern aber keine konstante Ausgangsspannung sondern eine, die abhängig von der Rotorlage ist. Diese Sensoren zur Rotorlagemessung sind meist direkt auf der Achse montiert.
Generell ist die Information der Rotorlage bedeutsam, um die Wicklung jederzeit effektiv und passend zur Lage des Rotors anzusteuern. Dieses Prinzip wird oft auch als elektronische Kommutierung bezeichnet.
Standardmäßig wird in jedem hochwertigen und hoch ausgelastetem Elektromotor die Temperatur an kritischen Stellen der Wicklung erfasst. Die Kontrolle der Temperatur kann potenzielle Schwierigkeiten frühzeitig erfassen und Warnmeldungen oder sogar die Abschaltung veranlassen. Noch wichtiger ist aber die Optimierung hinsichtlich der Ausnutzung des Motors: bis zum Erreichen eines als kritisch festgelegten Grenzwertes kann der Antrieb überlastet werden, um etwa die bestmögliche Beschleunigung zu erzielen.
Strom und Spannung
Die elektrische Leistung ergibt sich aus dem Produkt von Spannung und Strom. Für eine hohe Leistung wie beim Antrieb eines Elektroautos benötigt man also große Werte für Spannung und/oder Strom. Um einen hohen Strom verlustarm übertragen zu können, benötigt man dicke Kupferleitungen. Diese sind schwer und kosten viel Geld.
Erhöht man aber die Spannung zu sehr, stößt man an die Grenzen der Isolationsfähigkeit z.B. der Kupferlackdrähte. Folglich muss dann die Isolierung aufwändig verstärkt werden. Wie so oft liegt also auch hier die Lösung in einem Kompromiss. Bei einer aufgenommenen Leistung von 100kW und einer typischen Spannung von 400V fließen durch die Wicklung eines Drehstrom-Elektromotors ca. 150A.
Das folgende Bild soll die Einordnung der typischen Spannung von mehreren hundert Volt für Elektroautos erläutern. In der Welt der Elektrotechnik gelten die Begriffe Nieder-, Mittel- und Hochspannung. Die Grenze zwischen Nieder- und Mittelspannung liegt bei 1.000V Wechselspannung bzw. 1.500V Gleichspannung. Diese Werte sind u.a. auch in europäischen Richtlinien verankert. Beim Bild beachte man die logarithmische Skalierung.
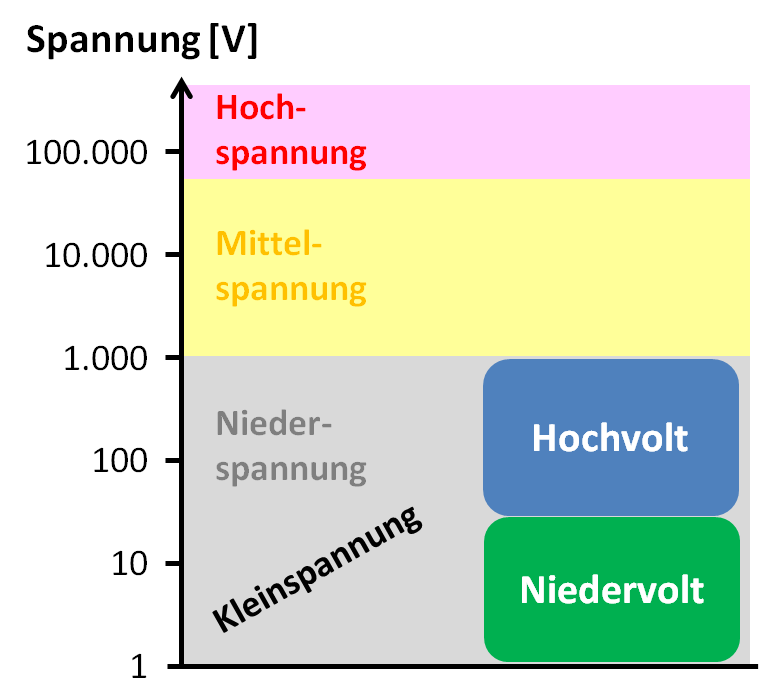
Die Grenze zur Hochspannung ist nicht ganz so klar definiert und liegt bei ca. 50 bis 60kV. Die Grenze zur Kleinspannung liegt bei einigen 10V und variiert je nach Gleich- oder Wechselspannung sowie den Umgebungsbedingungen. Hintergrund hierfür ist, dass Kleinspannungen als „berührungssicher“ gelten, d.h. von ihnen geht keine Gefahr für den Menschen aus.
Die Ebene der Niederspannung wird technisch angewandt in der Hausinstallation, bei Maschinen und Anlagen usw. Die Mittelspannung dient vorwiegend zur elektrischen Energieverteilung von Gemeinden und Stadtteilen sowie bei der Bahntechnik. Die Hochspannung schließlich wird für die Energieübertragung über weite Strecken (Überlandleitungen) verwendet.
Hochvolt-Technologie
Speziell für den Fahrzeugbereich wurden die Begriffe Hochvolt und Niedervolt eingeführt. Die Grenze liegt hier bei 30V Wechsel- bzw. 60V Gleichspannung. Motivation für diese neue Festlegung bei modernen elektrischen Antrieben war, dass eine klare Abgrenzung zu den bis dahin verwendeten ungefährlichen Spannungen erreicht werden sollte. Der Begriff „Hochvolt“ lässt schließlich eher eine Gefahr vermuten als „Niederspannung“.
Oftmals wird die Spannung eines Elektroantriebes von mehrern Hundert Volt als kritisch betrachtet. Nach meiner Meinung sind beim Elektroauto aber eher die hohen Ströme schwerer zu handhaben als die Spannung. Kabel- und Anschlussisolationen für diese Spannungsebene sind eigentlich recht unkompliziert zu gewährleisten.
Jede Motorwicklung muss an einem Übergabepunkt an ein elektrisches Kabel angeschlossen werden. Die Übergänge müssen dauerhaft und unter allen Umgebungsbedingungen – z.B. bei auftretenden Temperaturschwankungen oder unter mechanischer Belastung – in der Lage sein, die hohen Ströme zu führen.
Hochstromverbindungen werden meist geschraubt ausgeführt um eine ausreichend feste und großflächige Fügestelle zu erzielen. Dennoch bleiben Herausforderungen, wie etwa das Material der Schraube. Kupfer ist zwar gut leitfähig aber zu weich, Stahl dagegen hochfest aber ein schlechter Leiter. Messing oder Bronze bieten einen guten Kompromiss.
Bei einer gelockerten Schraubverbindung steigt lokal sehr begrenzt der Widerstand. Der Strom wird von der Leistungselektronik geregelt und bleibt konstant. Prozentual kann der Widerstand der gelockerten Verbindung stark ansteigen, z.B. von 0,1 auf 10mΩ. Dies führt bei einem Strom von 100A zu einer Verlustspannung von nur 1V, was messtechnisch schwer bis gar nicht erfassbar ist. Das Problem wird also von der Sensorik nicht erkannt.
Die lokale Verlustleistung steigt im gleichen Verhältnis wie der Widerstand, wodurch die Verbindungsstelle stark erwärmt wird. Durch diese Erwärmung steigt der Widerstand weiter an und damit auch die Verlustleistung. Falls die entstehende Wärme nicht mehr abgeführt werden kann, ist der Prozess instabil und sehr dynamisch. So kann die Verbindung sogar verflüssigen.
Fazit
Die eierlegende Wollmilchsau gibt es auch bei Elektromotoren nicht. Alle der in Elektrofahrzeugen eingesetzten Lösungen haben Vor- und Nachteile. Es gibt zwar auch andere Herausforderungen wie Verbindungstechnologie, Wickelkopfgeometrie und die Belastbarkeit der Isolation – die Kernfrage jeden Motors bleibt aber: wie bringt man möglichst viel Kupfer in die Nut?
Betrachtet man das Elektroauto als Ganzes, ist das Interessante an einer weiteren Effizienzsteigerung des Motors mit Sicherheit nicht die Erhöhung der Reichweite. Denn eine sinnvoll erreichbare Optimierung wird immer im niedrigen einstelligen Prozentbereich liegen. Vielmehr liegt der Hauptanreiz in der Reduzierung der Verlustleistung, einer dann einfacheren Kühlung sowie kompakteren Bauweise. Teilweise kann man also durch die Optimierung an anderer Stelle wieder Kosten einsparen.
Abschließend möchte ich die Tatsache betrachten, dass die Hersteller nicht besonders offensiv mit einer Beschreibung technologischer Features ihres Elektromotors umgehen – v.a. wenn man dies mit Verbrennungsmotoren vergleicht. Ich bin der Ansicht, dass das Wissen um die wesentlichen Aspekte des Designs und der Fertigung von Elektromotoren weit verbreitet ist. Neuentwicklungen und Fortschritte zeichnen sich meist eher durch Kombinationen mehrerer gut bekannter Maßnahmen aus oder liegen in der Weiterentwicklung von detaillierten Teilaspekten.
Dadurch wird es für die meisten Hersteller stets ein Leichtes sein, bei bekannter Ausführung von Konkurrenzdesigns diese mit relativ geringem Entwicklungsaufwand zu kopieren. Ich kann mich noch gut daran erinnern, wie schnell die Idee einer Einzelzahnwicklung von vielen Herstellern fast gleichzeitig umgesetzt wurde.
So stehen dem technisch versierten Besitzer eines Elektroautos also meist nur grobe Daten des Antriebes zur Verfügung. Dagegen werden viele nicht allzu interessierte Fahrer noch nicht einmal spontan beantworten können, ob ein ASM oder PSM verbaut ist. Im Falle eines PSM informiert der Hersteller aber noch nicht einmal über das Material der Permanentmagnete.
Ich muss zugeben, dass „elektronisch geregelte Schubumluftventile“ (O-Ton Mercedes, AMG) cooler klingen als ein „elektrischer Nuten-Füllfaktor von über 50%“. Hinzu kommt, dass viele Leute zumindest vorgeben oder sich so einschätzen, bei Verbrennungsmotoren über fundierte Kenntnisse zu verfügen – bei Elektromotoren aber gar kein Interesse vorliegt, dieses Wissen zu erlangen…